Oct 24, 2023
Make.Ship.Happen.® Part 9: Managing Cold Chain Logistics [CUSTOMER SPOTLIGHT]
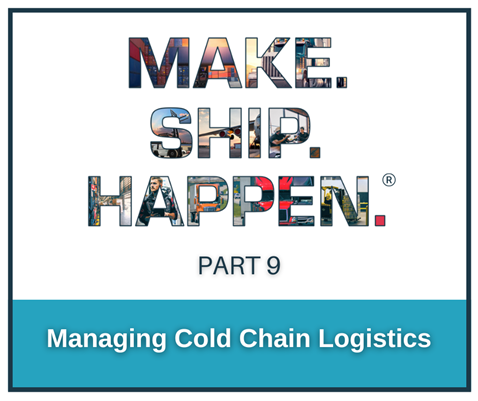
We’re back with the final (for now) installment of our Make.Ship.Happen.® series. This series has showcased a few of the ways that we at TA Services Make.Ship.Happen. every day, from guiding the carrier-shipper relationship to navigating LTL rules tariffs and international shipping. In our last post, we shared two case studies, one about implementing technology to improve warehousing operations and another on how partnering with a 3PL can help bridge the gap in supply chain software communications. Today’s last installment is tackling the complex world of cold chain logistics.
Cold chain management has unique and intricate challenges: maintaining strict temperature controls, delivering products with stringent time-sensitive deadlines, optimizing and understanding product seasonality, and managing costs to name a few. At TA Services, we have a comprehensive understanding of the requirements, rules, and regulations that are associated with managing an efficient cold chain. We build strong relationships with our customers in order to understand their businesses and unique needs. This allows us to address the challenges that come with cold chain management.
ICYMI: We recently published a customer spotlight on D’Arrigo Bros Co. where we talked about the complexities of cold chain management. Be sure to read the full story to see how TA Services and D’Arrigo Bros Co. have created a long-standing relationship built on trust and a commitment to service.
Complexities of Cold Chain Management
Temperature Control
It’s crucial to maintain the correct temperature for perishable products throughout the entire shipping process. Significant changes in temperature at any point in the supply chain journey can lead to damaged or destroyed products which equate to serious financial losses.
Time Sensitivity
Perishable products may have a limited shelf life or suffer diminished quality if not delivered in a timely manner. Meeting delivery deadlines is critical. Shipments must conform to a strict schedule to prevent expired or low-quality products being delivered to their final destination.
Cost Management
The need for specialized equipment to control temperatures, strict conformance to unique rules and regulations, and adherence to delivery times driven by product specifications can all add to additional costs not often associated with products transported without similar restrictions. Shippers must optimize their supply chain to minimize costs while still meeting temperature control and time sensitivity requirements.
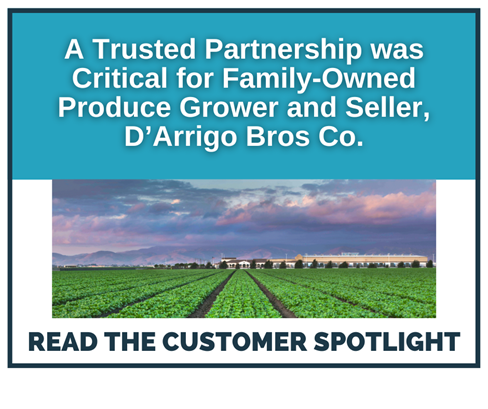
Reach out to TA Services today to learn more about our cold chain management solutions and the benefits of partnering with our experienced team.